INTRODUCTION
The ankle joint can be considered an essential part of human movement as it supports the entire body’s weight ( Li et al., 2021). Because of this, it is also frequently subjected to common injuries such as sprains and fractures. These injuries greatly affect the patient’s mobility. Rehabilitation and motion assistance at the early stage are necessary to help regain full mobility ( Chen et al., 2019). Physiotherapist usually performs the rehabilitation movement in one-on-one sessions because full attention from the physiotherapist is required. Passive motion for patients with injured ankles during ankle rehabilitation exercises includes adduction–abduction, dorsiflexion–plantarflexion and inversion–eversion motions. Thus, to enable a physiotherapist to attempt multiple patients simultaneously, a robot-aid rehabilitation device is an efficient alternative. This device could potentially help the physiotherapist teleoperate the robots from a remote location.
Several research works have reported the feasibility of the robot for assisting patients in recovering their ankle mobility ( Shi et al., 2019; Kian et al., 2022). However, most of these robots for ankle rehabilitation are based on static platform designs. These solutions require patients to be capable of standing up and are featured with devices that are large and immobile ( Jamwal et al., 2016; Chang and Zhang, 2019; Zhang et al., 2019). To overcome this limitation, ankle exoskeletons and orthoses are examples of wearable designs that have been proposed by several research works ( Cafolla et al., 2018; Cafolla et al., 2019; Zuccon et al., 2020). These wearable rehabilitation systems are heavy and stiff, though, and still need support from the sides to support their weight. Due to their lightweight construction, cable-driven robots might offer a solution to this problem ( Cafolla et al., 2018). Cable-driven mechanisms provide a higher payload-to-weight ratio, and the design can be made lighter compared to rigid-based robots ( Laribi and Ceccarelli, 2021). They have brought forward static (non-portable) designs for ankle rehabilitation ( Shahrol et al., 2018; Laribi and Ceccarelli, 2021).
A restrained platform is described in the following report ( Von Teh et al., 2020). However, due to the proposed device’s attachment to the patient’s foot rather than the shank, its four cables are insufficient to permit complete control of the ankle joint. Hence, the present study was undertaken to develop a conceptual design of a cable-driven ankle rehabilitation robot for bedridden patients that is capable of total control of the ankle joint. Before designing the conceptual robot, the specific requirements and problems of the cable-driven ankle rehabilitation robot must be identified and solved for this work. By focusing on the biomechanics of the human ankle joint’s mobility, the motion requirements were established.
The aim of this study is to develop a novel conceptual design for a cable-driven ankle rehabilitation robot specifically tailored for bedridden patients. The proposed robot must overcome the limitations of existing static platform designs and wearable systems by providing total control of the ankle joint while remaining lightweight and portable. To achieve this aim, the specific requirements and challenges of the cable-driven ankle rehabilitation robot must be identified and addressed. By focusing on the biomechanics of the human ankle joint’s mobility, the motion requirements for effective ankle rehabilitation will be established.
METHODOLOGY
Human ankle motion requirements
The range of motion (ROM) for assistance in smaller ranges is considered mainly for rehabilitation applications as well as assisting the elderly. The movements the ankle must accomplish are considered in the requirements for design and operation. The ankle would move in the desired manner entirely passively.
In unloaded ankle motion (in air), the action size can range from 1 to 20 N and can be scaled up to 100 N if the user is putting load on the foot. The usage of this device is planned for bedridden patients where the ankle is unloaded (no pressure is put on the feet). With exercise training being done to strengthen the ankle muscular system, it can be assumed that the force required for the device’s development is <30 N.
According to Saglia et al. (2013), only two rotational degrees of freedom (DOFs) are needed for exercises of the ankle. However, it can be observed that some ankle rehabilitation robots utilize 3 DOFs and 4 DOFs in their design.
Design criteria for concept generation
The main desired criterion for this device is to focus on ankle rehabilitation devices that can be worn and operated on a bedridden patient; therefore, mobility is not the main concern. However, the priority criteria for the conceptual design of this device are safety, portability, ease to use and treatment efficacy.
In figuring out the configuration of the device, consideration has been made to the mechanism design, actuation system and user interface (UI). Since it is desired for the ankle rehabilitation robot to be portable, the pneumatic system might not fit the criteria. Pneumatic actuation requires a compressor, which increases the number of equipment needed for the device to operate. Using an electrical actuator remedies the issues of portability.
The assessment of the desired criteria of the bedridden ankle rehabilitation device was made in comparison to the current existing robot-aided ankle rehabilitation devices. These devices are the Wearable Ankle Rehabilitation Robotic Device, the Optimal Design of Cable Driven Ankle Rehabilitation Robot (ARBOT) and the Optimal Design of Cable Driven Ankle Rehabilitation Robot ( Saglia et al., 2013; Von Teh et al., 2020). The description of assessment criteria is available in Appendix 1.
Morphological chart
The criteria required for designing the ankle rehabilitation robot generated by the morphological chart are listed in Table 1. Five concept designs were generated by mixing and matching the criteria.
Morphological chart.
Criteria | Parameters | ||||
---|---|---|---|---|---|
Brace type |
![]() Flipflop/sandal |
![]() Foot plate |
![]() Heel brace |
![]() Full brace |
![]() Toe-socks/compress |
Mechanism | Screw mechanism | Helical gear
Pneumatic | Belts
Cams | Lever mechanism
Peaucellier cell | Cables
PAM (pneumatic artificial muscle) |
2-way cylinder
Spring mechanism | Shafts and gears
Hydraulic | Internal gear
Swing arm quick return | Spur gears
Rack and pinion | Pulleys | |
Actuation point | Flex muscle (front) | Flex muscle (back) | Relax muscle | Horizontal muscle (on ankle) | Flex and relax (front and back) |
Actuator | DC rotary motor
PMA (pneumatic muscle actuator) | Solenoids | Hydraulic cylinder | Shape memory alloy | SEA (series elastic actuator) |
Torque application |
![]() Tension near toes |
![]() Midfoot tension |
![]() Pulleys |
![]() Gear near ankle |
![]() Attached muscle |
Interface | PC | Control panel (wire connection) | Remote control (wireless transmission) | ||
Sensors | Force sensor | Optical encoder | Pressure sensor | Linear potentiometer | Displacement sensor |
Torque sensor | Magnetic rotary encoder | Axis inclinometers | Proximity sensor | Accelerometer | |
DOF | 1 | 2 | 3 | 4 | 4 |
Materials | Plastic | Aluminium | Nylon | Neoprene
Fibreglass | Spandex |
Abbreviation: DOF, degrees of freedom.
Selection criteria
Table 2 shows the selection criteria for the ideal concept design that was generated. These criteria were considered as a basis for the overall ankle rehabilitation robot’s usability.
Selection criteria.
Criteria item | Description |
---|---|
Easy to build | Ease of technology and implementation |
Cost effective | Applicable for both production and prototyping |
Ease of application | Easy for user to apply and with one person |
Comfortable | Pressure, heat, weight, etc. |
User friendly | Interface eases uses and easy to adjust |
Effective | Adequate performance to accomplish proper ankle treatment exercises and motion |
Reconfigurable | Can adjust manually or automatically |
Safe | Safe for operation and build |
Portability | Ease of use at different location with little adjustment |
Pugh chart concept selection
The Pugh method was utilized for the selection of the conceptual design of the ankle rehabilitation device. This method is typically employed to decide on a design at the early conceptual design stage. It is a graphical method that employs a matrix with columns for the concept and rows for the decision criteria. With this approach, the best concept design was chosen.
The reference design (Datum) is a 3-DOF ankle rehabilitation robot developed by Jamwal et al. (2016) and was compared with another concept design. Each concept design was compared to the Datum. The score will be zero if the concept design’s criteria match those of the Datum. The design will receive a +1 if it is superior to the Datum. A score of −1 is given when the concept design is inferior to the Datum. Table 3 lists the concept design selection based on the Pugh method, while Table 4 lists the scale for concept design selection.
Pugh method for concept design selection.
Function | Datum | Concept design | ||||
---|---|---|---|---|---|---|
A | B | C | D | E | ||
Secure foot | Steel platform | Shank brace with foot plate | Full brace | Toe-socks/compress | Heel brace | Shank brace with foot plate |
Mechanism | Pulleys | Bowden cable | Spring mechanism | Pulleys | 2-way cylinder | Air muscle |
Actuator | DC motor | DC motor | DC motor | SEA | PMA | Soft pneumatic actuator |
Actuate muscle | Flex and relax (front and back) | Flex and relax (front and back) | Flex muscle (front) | Horizontal muscle (on ankle) | Flex muscle (back) | Flex muscle (back) |
Torque application | Platform under foot | Pulleys | Midfoot tension | Attached muscle | Gear near ankle | Tension near heel |
Interface System | PC | PC | Sound | PC | Remote control | Control panel |
Sense motion data | Force sensor and accelerometer | Accelerometer and IMU | Displacement and torque sensor | Optical encoder and pressure sensor | Proximity sensor | Accelerometer and force sensor |
DOF | 4 | 3 | 3 | 3 | 2 | 2 |
Material | Steel | Nylon and plastics | Steel and nylon | Neoprene, spandex, and fibreglass | Nylon | Neoprene and fibreglass. |
Abbreviations: DOF, degrees of freedom; PMA, pneumatic muscle actuator; SEA, series elastic actuator.
Inverse kinematics
The proposed cable-driven robot’s inverse kinematics are comparatively straightforward and offer a singular cable length solution for a specific end effector pose. The moving platform (MP) pose shown in Figure 1 was used to calculate the wire lengths used in the discussion that follows.
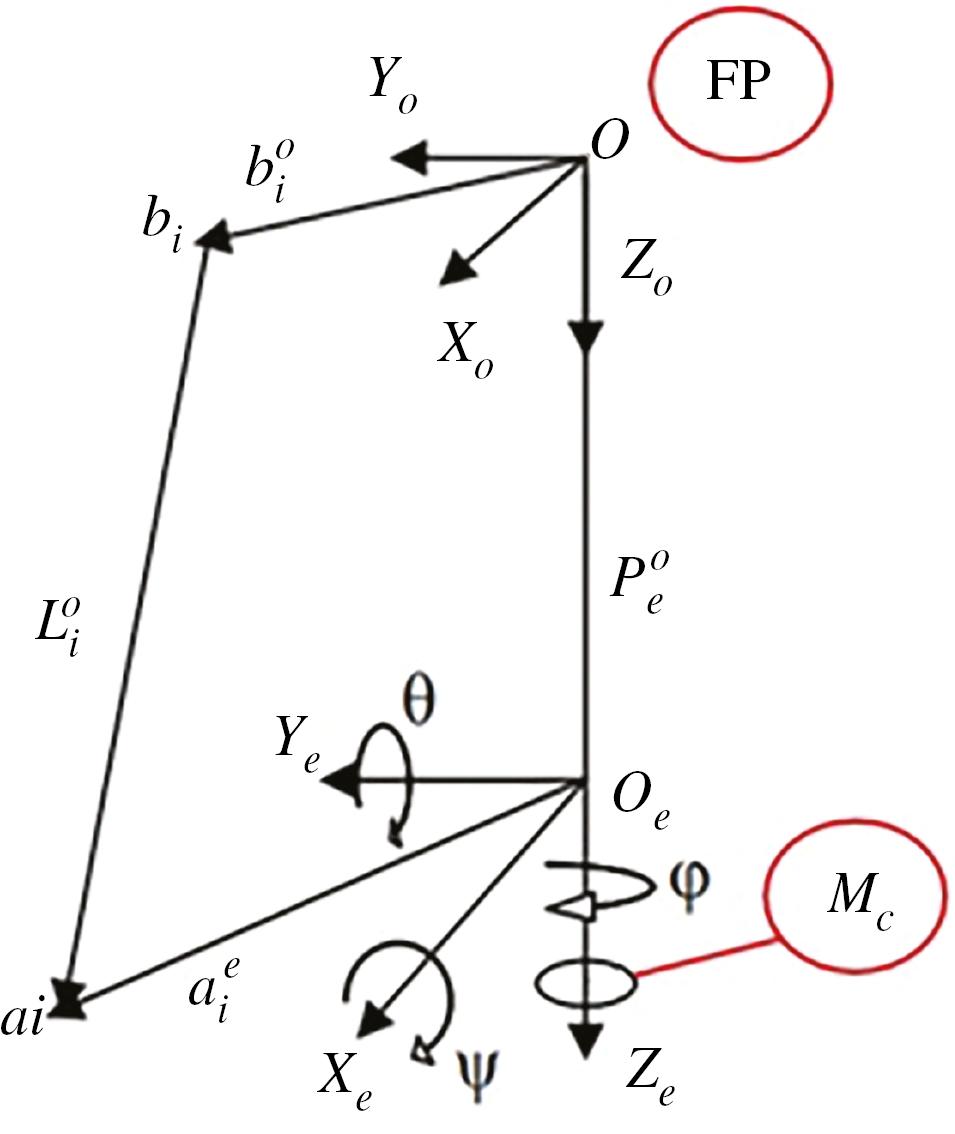
A sketch of cable and position vectors of connection points on the fixed shank platform and moving foot platform ( Jamwal et al., 2016).
A spherical joint with limited angular motion can estimate the kinematic behavior of the ankle motion. Using an S-4SPS architecture, the proposed solution can be modeled as a lower-mobility parallel mechanism with 3-DOF. The connection points between the MP and fixed platform (FP) are denoted by a′i s and b′i , respectively. The FP’s connection points are all in the same plane ( Z O = 0) and are located at a radial distance r b from the coordinate system at O. Position vectors (boi) of point b′i s on the FP are defined by equation (1):
where the radial distance from the origin, O, is indicated by r b . The variable β i displays the angle between the respective axes at which point b i on FP is located. The connecting points for the MP are similarly situated on a circle of radius r a , and the coordinate frame attached to O e is roughly 495 mm above the MP’s center of mass ( M c ) (with reference to the position of ankle joint which is about 495 mm above the moving plate level).
Equation (2) can be used to determine the position vectors (aei) of the four connection points on the MP:
The variable β i indicates the angle at which the point a i on the MP is in relation to each of its axes. As shown in equation (3), a system of four equations can be used to express the cable length position vectors in terms of end poses:
where Poe is the position vector of point O e relative to O. Roe is the rotational transformation matrix of MP with respect to FP using a fixed axis rotation sequence of and about the ψ, θ and ϕ and X o , Y o and Z o axes, respectively, and can be written as in equation (4):
RESULTS
The results obtained in this study can be discussed in four parts: (1) the generated concept from the morphological chart and Pugh method; (2) the selected design and the mechanism generated from the Pugh method; (3) the trajectory simulation of the chosen design; and (4) the performance analysis of the generated concept based on inverse kinematics.
Generation of conceptual design
Table 5 displays the five conceptual designs for ankle rehabilitation robots that have been created and visualized using SolidWorks based on the criteria of the morphological chart.
Comparison between the generated conceptual design.
Design | Dimension (cm) | DOF | Actuator | Mechanism | Interface | Sensor | Working mode |
---|---|---|---|---|---|---|---|
A | 50 × 10 × 25 | 3 | Stepper motor | Pulleys (Bowden cable) | PC | IMU | Lying/standing/sitting |
B | 31 × 26 × 40 | 3 | DC motor | Spring | Sound | Displacement | Sitting/standing |
C | 27 × 14 × 32 | 3 | SEA | Pulleys | PC | Optical and torque | Lying/standing/sitting |
D | 37 × 20 × 35 | 2 | Pneumatic | Pneumatic cylinder | PC | Proximity | Sitting/standing |
E | 34 × 15 × 25 | 2 | Soft pneumatic actuator | Air muscles | Control panel | Accelerometer and force | Lying/standing/sitting |
Abbreviations: DOF, degrees of freedom; SEA, series elastic actuator.
An ankle rehabilitation robot with a 3-DOF cable-driven parallel mechanism is Design A. The design measures 50 cm by 10 cm by 25 cm. On the sides of the foot plate, close to the ankle and toes, four Bowden cables with stepper motor mechanisms are attached to the shank strap. The motors will pull the Bowden cable to manipulate the moving foot platform. The design has an accelerometer and IMU sensors with a PC as the UI. This design uses nylon plastics, a soft strap for the adjustable part of the shank and a more solid piece for the foot plate. This design can perform ankle rehabilitation exercise motions like inversion, eversion, dorsiflexion, plantarflexion, adduction and abduction and is suitable for bedridden use.
Design B is a 3-DOF full-brace robot-aided ankle rehabilitation device. The dimensions are 31 cm × 26 cm × 40 cm. This device uses two spring mechanisms placed at the front and back of the foot plate to allow movement for dorsiflexion and plantarflexion. This robot uses a DC motor to actuate the springs. For ankle rehabilitation exercises in the sitting and standing modes, this design is better suited. Only plantarflexion and dorsiflexion ankle exercise motions are doable by this design. The ankle robot uses sound as the UI and has displacement sensors placed to detect the distance of placement. Design B is made of steel frame and nylon for padding.
Design C is a 3-DOF ankle rehabilitation robot. The dimensions of Design C are 27 cm × 14 cm × 32 cm. It has a toe-socks foot sleeve design. This design uses a series elastic actuator (SEA) for actuation of pulleys. Three pulleys are placed near the dorsum of the foot to replicate the movement of the dorsal muscles. This design allows for the practice of ankle rehabilitation exercise motions like inversion, eversion, dorsiflexion and plantarflexion. For gait sensing, optical encoder and torque sensors are used to detect and interpret robot movement. The PC is the UI for this robot. The robot in this design uses lightweight, sturdy materials such as neoprene, spandex and fiberglass for the frame. This design is good for bedridden patients’ use as it can function in any position.
Design D is a 2-DOF heel brace ankle rehabilitation robot with dimensions 37 cm × 20 cm × 35 cm. This device uses a two-way pneumatic cylinder mechanism. This device can perform plantar flexion and dorsiflexion ankle rehabilitation exercises. It can be used in sitting and standing positions, though using this design while lying down might not be feasible due to the pneumatic requirements. This ankle robot uses nylon for the brace padding and plastic for the frame. It has a proximity sensor to detect gait.
Design E is a 2-DOF over-actuated parallel mechanism ankle rehabilitation robot with dimensions 34 cm × 15 cm × 25 cm. It is a shank brace with a foot plate design. The robot uses air muscles affixed to the sides and back of the brace actuated by a soft pneumatic actuator. The robot can perform dorsiflexion/plantarflexion and eversion/inversion ankle motions. This device can be worn for standing and bedridden uses. It uses accelerometer and force sensor for motion detection and a control panel as the UI. The materials used for this device are neoprene and fiberglass.
From the generated selection criteria, the weights of each criterion were given, and points attributed to each criterion were generated as the table against the Datum. Based on the generated designs, the selection criteria are compared, and points are given. Designs with better than the Datum get a positive point, and the magnitude of the point dictates how good the design is. From Table 6, it can be observed that Design A has criteria that are the best. The design has a simple build, and that also means that it is cost effective as well. It did not score well for comfort, but its simplistic build meant that it is user-friendly. Criteria that are the same as the Datum are scored at zero (0).
Selection criteria for the chosen design.
Selection criteria | Datum | A | B | C | D | E |
---|---|---|---|---|---|---|
Easy to build | 3-DOF ankle robot | +2 | +1 | −1 | +1 | +1 |
Cost effective | +2 | 0 | −2 | −1 | +1 | |
Ease of application | +2 | +1 | −1 | +1 | +1 | |
Comfortable | +1 | +1 | +2 | +1 | 0 | |
User friendly | +2 | +1 | +1 | +1 | +1 | |
Effective | 0 | 0 | 0 | 0 | 0 | |
Reconfigurable | +1 | −1 | −1 | +1 | +1 | |
Safe | +2 | +1 | +2 | +2 | +2 | |
Portability | +2 | +1 | +2 | +2 | +2 |
Abbreviation: DOF, degrees of freedom.
Selected design
The ankle robot is designed to give the ankle joint 3 DOFs in rotation. The apparatus has two parallel platforms: one FP affixed to the shank and a moving foot platform where the foot is placed. The leg support structure is ring-shaped or straps that is fixed to patient’s leg. The cable lengths are varied by the motors. The overview revealing the conceptual layout of the wearable ankle rehabilitation device with main components and corresponding 3D model of the proposed conceptual design are presented in Figures 2 and 3 respectively.
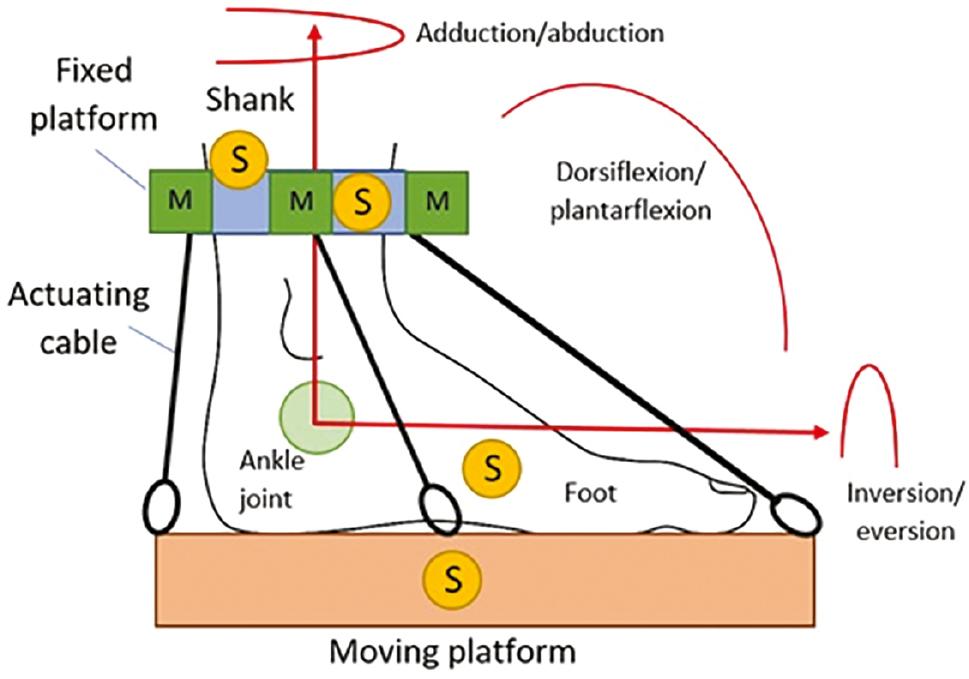
Proposed design: Conceptual layout of the wearable ankle rehabilitation device with the main components.
A mechanical structure with Bowden cables and servomotor will guide the relative motion of the cables. For the operational control of the device, sensors can be used. These sensors may also provide monitoring for ankle medical issues, such as muscle reaction, blood pressure and stiffness measurement. Sensors can also be installed on the device itself or worn by the patient to provide information for the control system. These sensors, which enable gait analysis, include accelerometers and IMUs, as reported in Jamwal et al. (2016).
Generation of MATLAB model
MATLAB model for the proposed design of the ankle robot is shown in Figure 4. This model is developed based on the inverse kinematic analysis that has been performed. The actuation cables are positioned at the FP in Figure 5 as a base and attached to the MP to allow movement for the affected foot. The actuation cable used in this mechanism is proposed to be Bowden cable mechanism, where the FP attached to the shank will serve as the base of the moving Bowden cable, and an external motor will perform the pulling motion to permit motion on the MP.
The fixed points are placed at the blue dots. This MATLAB model is made according to the dimensions of Concept Design A. Therefore, equation (2) was used to determine the new vector position for the MP after motions of the ankle have been performed.
Trajectory simulation
The trajectory simulation for the MATLAB model of the ankle rehabilitation robot is first set at the origin position, as shown in Figure 6. This origin position is at (−250, −100, 0) for a 1; (100, −100, 0) for a 2; (−250, 100, 0) for a 3; and (100, 100, 0) for a 4. The trajectory simulation presented with this MATLAB simulation is based on the 3D SolidWorks design proposed and the inverse kinematics derived from the design. The values for the angles used are based on the required ROM exercises that are effective for ankle rehabilitation. These ranges are simulated from Figures 7 to 10 for the inversion, eversion, dorsiflexion, plantarflexion and abduction motions. The initial position for the MP is represented by the black rectangular, while the new position after angle values are placed is represented by the blue rectangle. The green dotted lines represent the cables attached to the two platforms. The red rectangle represents the FP that bounds the motion of the cables and MP.
Cable length analysis
Table 7 shows the cable length for all the axes of the ROM consisting of the inversion/eversion on the x-axis, dorsiflexion/plantarflexion on the y-axis and adduction/abduction on the z-axis. The result shows that the longest cable extension at any ROM for the ankle robot is at plantarflexion with 411.1228 mm extension on the −45 degree angle for both L1 and L3. Meanwhile, the shortest cable retraction is in the same range for L2 and L4 at 183.0615 mm.
Cable length for all axes maximum and minimum.
Axes | Range of motion | Angle (degrees) | (mm) | |||
---|---|---|---|---|---|---|
L1 | L2 | L3 | L4 | |||
0 | Origin | 0 | 307.5759 | 307.2163 | 307.2163 | 307.5759 |
x | Inversion | 14.5 | 345.2694 | 279.3925 | 267.4697 | 230.2655 |
22 | 363.3602 | 291.1930 | 246.3893 | 217.5609 | ||
Eversion | −10 | 280.0725 | 238.0053 | 333.9195 | 272.0502 | |
−17 | 260.4416 | 225.9944 | 351.4196 | 283.3913 | ||
y | Dorsiflexion | 20 | 252.0047 | 288.1054 | 252.0047 | 288.1054 |
30 | 224.1741 | 303.0548 | 224.1741 | 303.0548 | ||
Plantarflexion | −37 | 393.9524 | 193.9330 | 395.9524 | 193.9330 | |
−45 | 411.1228 | 183.0615 | 411.1228 | 183.0615 | ||
z | Adduction | 22 | 313.2657 | 258.8257 | 313.267 | 258.8257 |
35 | 321.5218 | 264.0897 | 321.5218 | 264.0897 | ||
Abduction | −15 | 310.2514 | 256.9116 | 310.2514 | 256.9116 | |
−25 | 314.8780 | 259.8512 | 314.8780 | 259.8512 |
DISCUSSION AND CONCLUSION
In this study, Design A was selected from five other generated designs using the morphological chart where the features required and needed were picked from an array of possible selection of features. Using the Pugh method to select the best design generated from the morphological chart, careful consideration was given in the selection process.
The finalized design consists of a parallel cable-driven robot with an FP attached to the leg’s shank acting as the FP, and an MP, or end effector, located at the foot. This design uses Bowden cables for actuation where the external actuation is done with a DC motor. This design is suitable for different positions whether for bedridden use, standing or sitting. With the actuator not being attached directly to the orthosis itself, the system allows for more comfort as there is no cumbersome mechanism attached to the ankle robot itself. The design uses sliders as a proponent for the structural integrity of the ankle rehabilitation robot. From the generated 3D design using SolidWorks, the kinematic model, the inverse kinematic model was then developed to have the mathematical models plugged into MATLAB, where a simulation was then programmed using the plot3 functions to represent the platforms and projected cable behavior of the robot.
In this simulation, the three axes of ankle motion—inversion/eversion, dorsiflexion/plantarflexion and abduction/adduction—were used to represent the lengthening of the cable and test the viability of a robot design for achieving the required ROM exercises. From the MATLAB simulation and the data derived from the program, it can be observed that Concept Design A could achieve the full ROM for effective ankle rehabilitation exercises. In conclusion, this ankle robot rehabilitation design is successful in fulfilling the design requirements for an effective ankle rehabilitation robot.